Extrusion is an industrial moulding process used in many sectors to produce objects from a wide range of materials, including polymers, metals, foodstuffs and especially rubber (one of our articles is devoted entirely to rubber extrusion).
The process offers flexible and efficient solutions for manufacturing products in large quantities, while allowing precise customisation of shape and material properties.
How Extrusion works
The extrusion process is based on the idea of forcing a heated or semi-solid material through a die (mould) to give it a specific shape. The different stages are described below:
1. Feeding: The process begins with the raw material being fed into the extruder. This can be in the form of powder, granules or paste, depending on its properties and intended application.
2. Melting and homogenisation: Inside the extruder, the material is gradually heated and melted by the action of one or more rotating screws. This crucial stage not only melts the material, but also homogenises it, guaranteeing consistent quality in the final product.
3. Forming: The material is forced under pressure through a die. The geometry of this die determines the final shape of the extruded product, whether it is a sheet, tube or complex profile.
4. Post-treatment : Immediately after passing through the die, the extruded product is subjected to heat treatments, which may include gradual cooling or annealing depending on the material and the intended application, to ensure optimum geometric and functional specifications.
5. Finishing: Depending on the specifications of the final product, extrusion may be followed by additional operations such as cutting to length or winding for continuous products.
Extrusion process variants
There are several types of extrusion, each adapted to specific materials and applications:
- Hot extrusion: Used mainly for plastics, metals and rubber, this process involves heating the material to make it malleable before passing it through the die.
- Cold extrusion: Mainly used for metals, this technique involves extruding the material at room temperature, thereby preserving its mechanical properties.
There are also two main approaches to extrusion: continuous and semi-continuous.
Continuous extrusion produces the material without interrupting the material flow, while semi-continuous extrusion produces a series of separate parts.
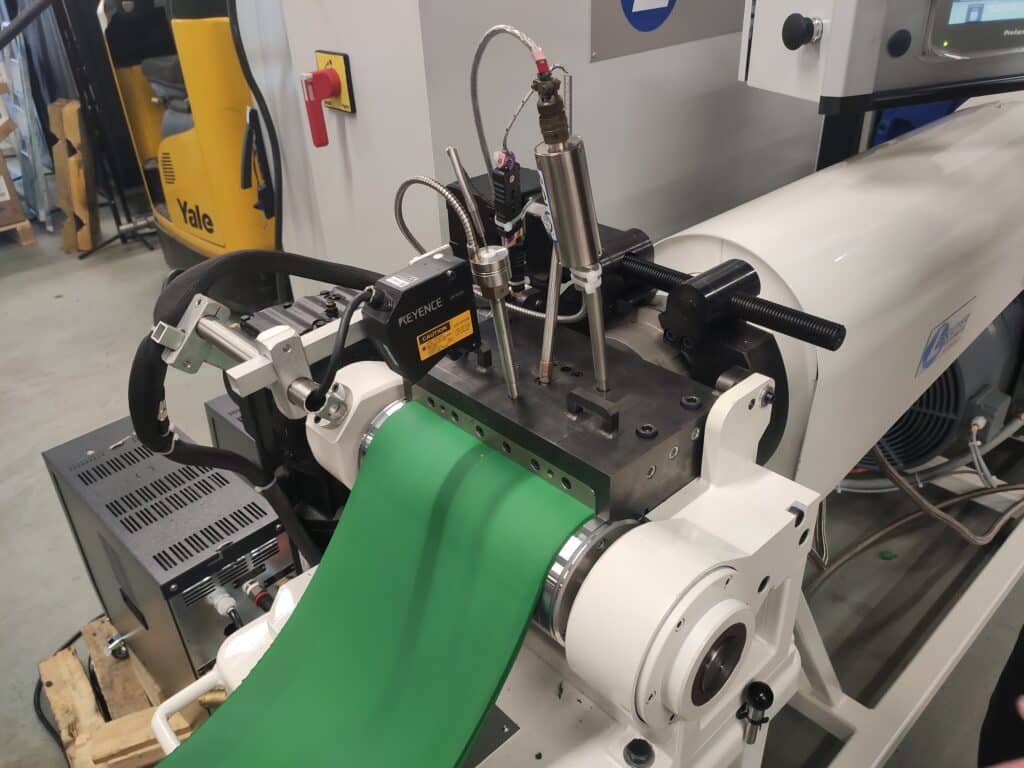
Finished products from the extrusion process
Extrusion is used to produce a wide range of items and products used in many industries. Here are some typical examples of extruded products:
- Tubes and pipes: Used in the construction, plumbing and automotive sectors, extruded pipes are made from plastic or metal, depending on the need for durability or flexibility.
- Profiles: Extruded profiles, whether plastic or metal, are used in the construction of windows, frames and other architectural structures.
- Plastic films: Often used for food or industrial packaging, plastic films are produced continuously by extrusion, ensuring thin, uniform layers.
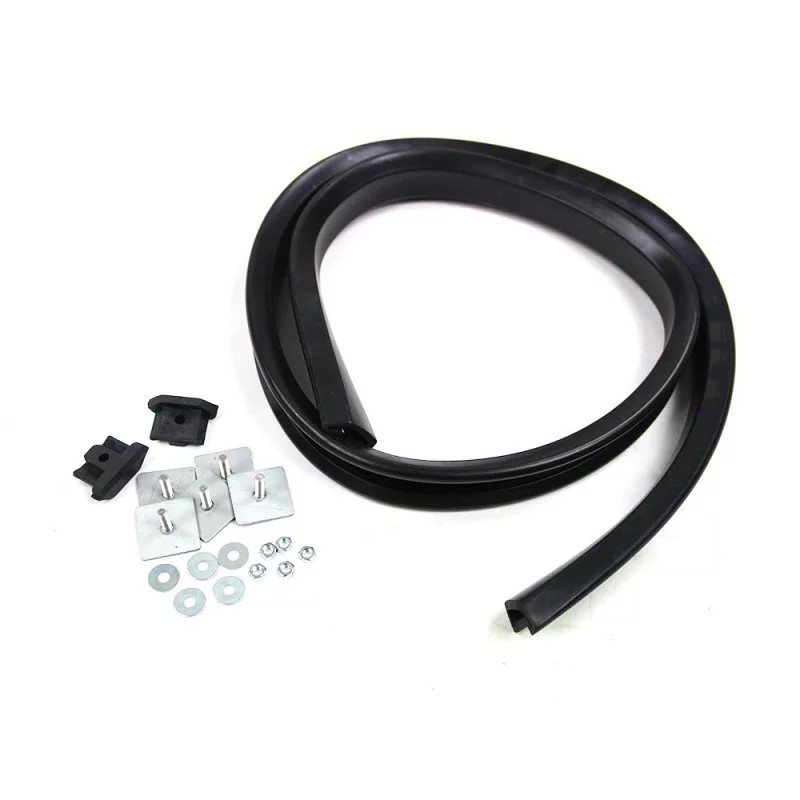
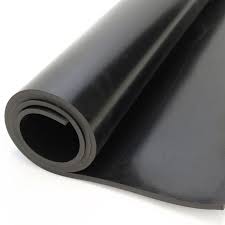
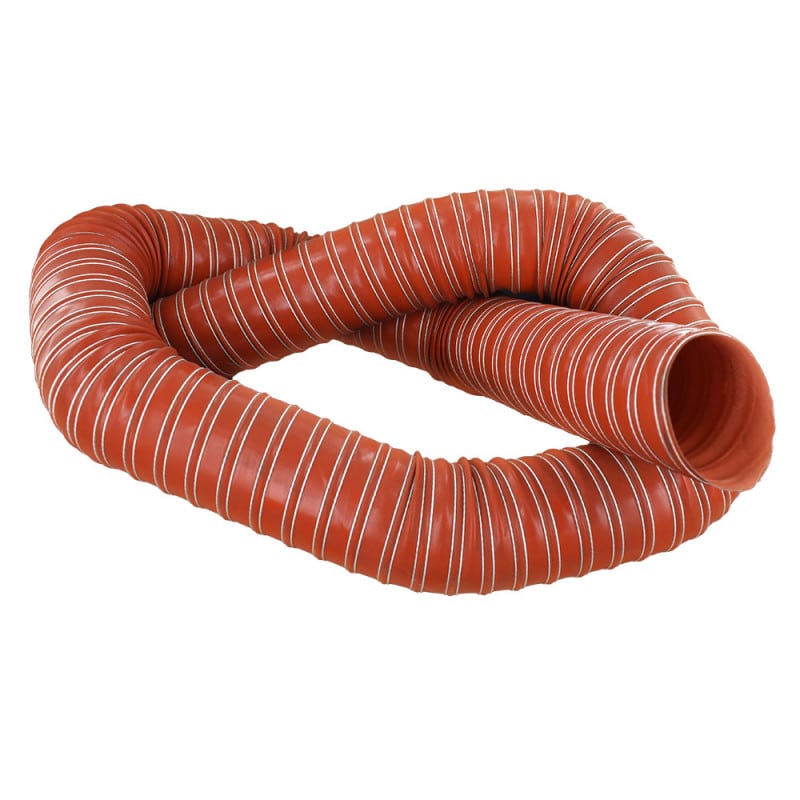
The outlook
The extrusion process continues to evolve through the integration of new technologies. Recent advances in composite materials and improvements in energy efficiency are increasing the importance of extrusion in the industry. In addition, the increasing use of recycled materials is opening up new prospects for the sustainable production of extruded products.
Rubber extrusion is also at the forefront of innovation, for example, Lescuyer & Villeneuve has patented a filter-degasser extruder that combines filtration and continuous degassing.