Extrusion is an industrial process used to transform materials, mainly polymers, metals or foodstuffs, by forcing them through a die or orifice that gives them a defined shape.
A more general article on the extrusion process is available on our blog!
We use this process extensively in a wide range of industries, including the automotive, food, construction and other sectors.
Rubber, a unique polymer for extrusion
Rubber, a natural polymer, has remarkable elastic properties, exceptional wear resistance and the ability to absorb shock.
Unlike synthetic polymers such as plastics, rubber extrusion requires a crucial additional step: vulcanization.
This chemical process, which involves heating the rubber in the presence of sulphur, gives the material its final properties of elasticity and strength. There are several key stages in rubber extrusion:
1. Material preparation: Raw rubber is mixed with various additives, such as vulcanising agents, fillers, antioxidants and pigments. This mixture must be carefully formulated to ensure optimum vulcanisation.
2. Material temperature: The extrusion temperature must be precisely controlled, at lower temperatures than for thermoplastics, to avoid pre-vulcanisation in the extruder.
3. The extrusion screw: Rubber screws are specially designed to handle the high viscosity and specific behaviour of the material.
4. Vulcanisation: After extrusion, the material is subjected to high temperatures (150-190°C) to stabilise its geometry and mechanical properties. This stage can be carried out in autoclaves, molten salt baths or hot air tunnels. You can find out more about this process on the MDC Engineering website.
Variety of possible applications
When rubber is extruded, it can be transformed into a wide variety of products for a wide range of industrial applications.
The main types of extruded product include:
- Tyres: Tyres are one of the most common products made from extruded rubber. Rubber compounds are extruded to form treads, which are then assembled to form the different layers of a tyre.
- Pipes and Tubes: Used in plumbing, irrigation and fluid delivery systems, extruded pipe is designed to withstand high pressures and varying environmental conditions.
- Profiles: Extruded profiles are widely used in the construction industry, particularly for windows, doors and load-bearing structures.
- Bands: Depending on the extrusion head selected, extrudates can be in the form of rubber strips or sheets. These sheets offer interesting properties such as flexibility, temperature and chemical resistance.
- Elastic components: In the case of rubber, extrusion is used to produce seals, belts and other flexible parts, ideal for industrial applications requiring good wear resistance.
- Common items: Rubber extrusion is also used to make items that we use frequently in our daily lives. These include gloves, which are widely used in the medical and industrial sectors, and shoe soles. Here, extrusion is used to produce items that are flexible, durable and suitable for a wide range of practical applications.
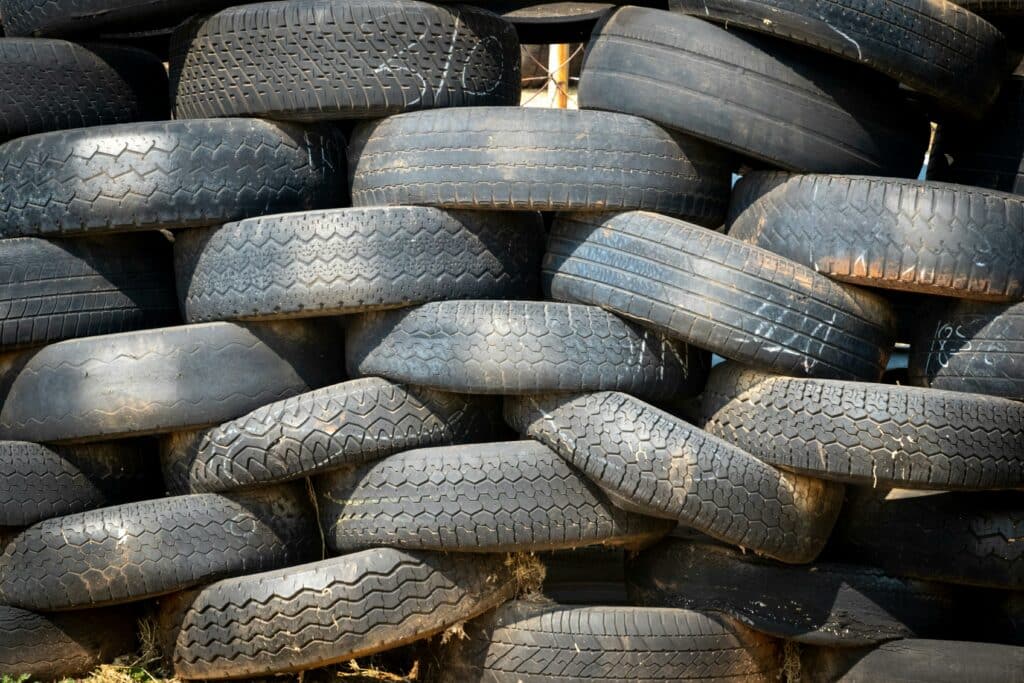
The various types of rubber extruder
The choice of extruder is critical to the production of high quality elastomer products. Each type of extruder offers specific advantages adapted to different elastomer formulations and applications. Here are the main types of extruders used to process elastomers, particularly rubber:
- Single screw extruder: A single screw is used to feed, melt and form the material. It is often used for standard applications where simple mixing of the material is sufficient. Single-screw extruders are particularly suitable for standard rubber compounds and are renowned for their efficiency and ease of operation.
- Twin screw extruder: With two parallel screws rotating in opposite directions, these machines offer improved mixing and precise temperature control. Ideal for complex formulations and heat-sensitive materials, they enable efficient processing of elastomers while ensuring uniform dispersion of additives.
- Conical screw extruder: Used for low-viscosity materials, conical screw extruders facilitate the transport and packaging of rubber. They are particularly effective in the production of small diameter profiles and tubes where precision is essential.
- Variable pitch screw extruder: This type of extruder allows the screw pitch to be varied during extrusion to match the changing properties of the material. This is particularly useful for complex elastomer formulations that require frequent adjustments to achieve optimum mechanical properties.
- Degassing filter extruder: Lescuyer & Villeneuve patented extruder combining filtration and continuous degassing. The level of material purity and yield is higher than with standard equipment.
- Pintle extruder: This extruder is useful for specific needs, particularly formulations that require more intensive mixing of additives.
- Co-extrusion line: Process for combining multiple polymer streams in a single production stream to create multilayer products with specific properties.
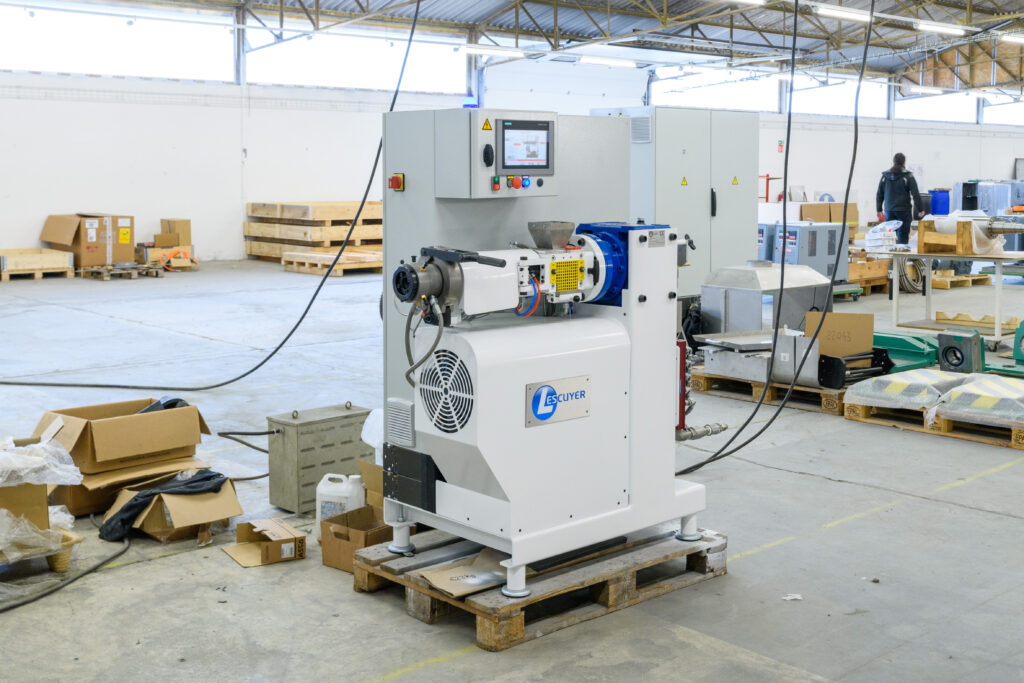
Benefits of rubber extrusion
Rubber extrusion is used to make products that are durable, flexible and resistant to temperature changes and mechanical stress. In the automotive sector, for example, rubber extrusion is often used to make seals, radiator hoses and protective bellows.
This process also enables the mass production of parts with precise dimensions, while ensuring the uniformity of the finished product.